‘Muda’ is the Japanese word for ‘waste’ and it is something which carmakers have always worked hard to minimise as it does not add value to a product or service. Muda can occur not only in production activities but also other activities like meetings or office work. Reduction of muda is therefore a way to lower costs and also improve quality.
Honda has long kept a focus on muda in its production activities and as an extension of that corporate discipline, it also sources materials for new products by recycling and reusing material from end-of-life vehicles and its operations.
The carmaker’s recycling initiative includes an initiative that takes used uniforms worn by associates (as Honda calls its employees) at its US manufacturing and R&D facilities and transforms them into sound-absorbing insulation for use in Honda and Acura vehicles.
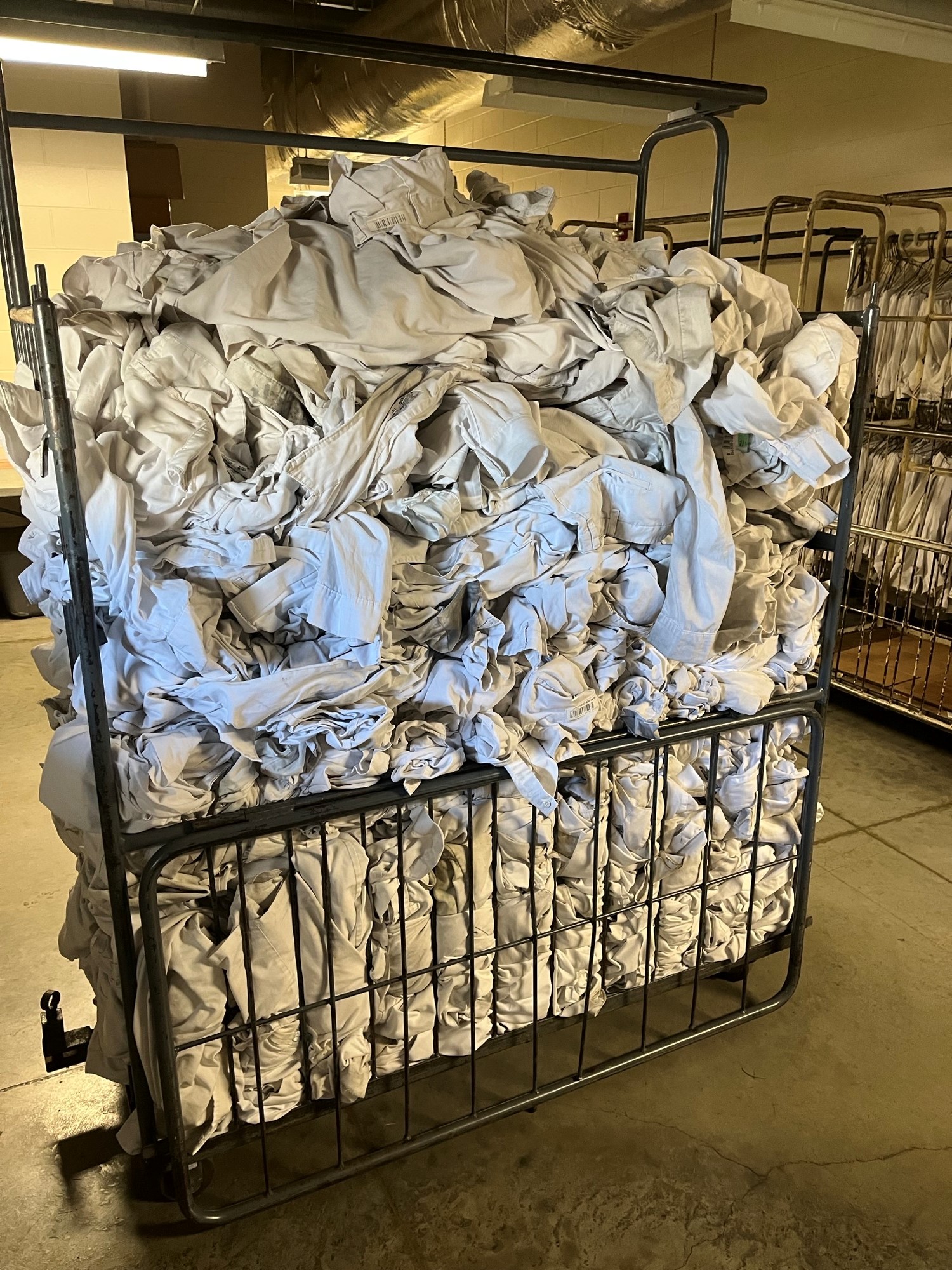
Less waste sent to landfills
Since the program began in 2021, almost 173,000 kgs of uniforms have been recycled. Each month, approximately 20,500 kgs of materials from the uniforms are diverted from reaching landfills.
“To achieve our Triple Zero goal of 100% sustainable material use, we need to take every possible opportunity to recycle materials at end of life for reuse in our products, thereby minimizing our utilization of virgin materials,” said Negar Gilsinger, Manager of Resource Circulation for American Honda Motor Co., Inc. “By maximizing end-of-life material recycling, we are giving our uniforms a second life in Honda and Acura vehicles.”
In collaboration with suppliers
The recycling program leverages cross-industry collaboration between Honda and its two uniform suppliers, as well as an insulation supplier and textile recycler. The uniforms, when no longer worn, are recycled and reused in 5 different insulator parts on all 9 Honda and 4 Acura models made in North America. In future, Honda plans to expand the uniform recycling program to other facilities in North America.
“Collaborating with Honda suppliers in the uniform recycling program has brought great value to our supply chain sustainability efforts,” said Rob Long, Senior Procurement Specialist with Honda North American Indirect Procurement. “As Honda works to advance sustainability, we appreciate our suppliers’ efforts to innovate their business operations to reduce waste and give new life to our Honda uniforms.”
How uniforms become insulation
The uniforms collected and cleaned by the suppliers are first evaluated after washing. If they are undamaged, they are sent back to associates to continue using. Those that are designated for reuse in vehicles will then be reprocessed and blended with fibre-based materials.
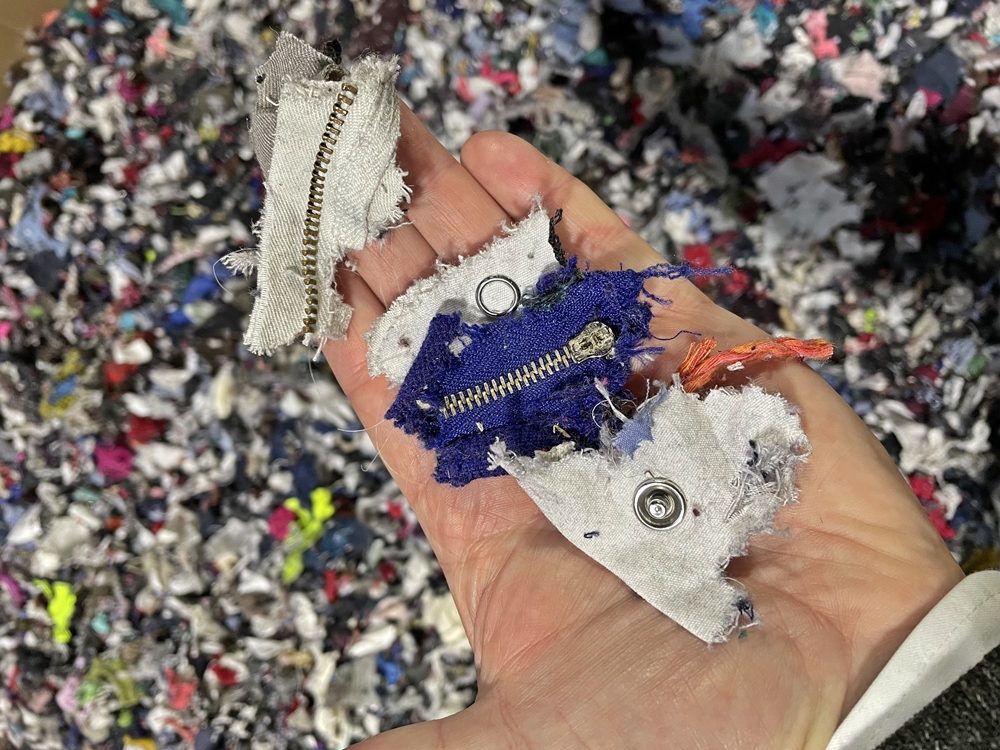
The reprocessing involves shredding to turn the uniforms into a material that meets the required fibre grade for use as insulators in vehicles. Zippers and buttons from the uniforms are extracted so that no metal or plastic goes through the shredding process. Then the material gets blended into mixed fibres and tested to ensure the material meets requirements.
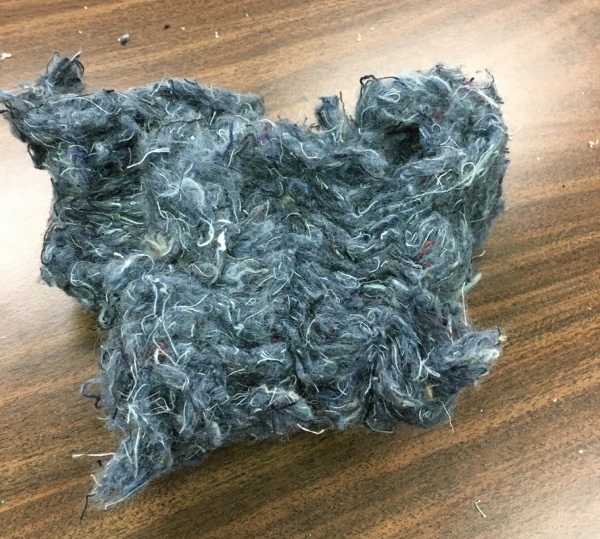
The newly reprocessed fibres are then packaged and delivered to the insulation supplier where they are turned into insulation and sent to Honda’s plants. Besides the uniforms, the insulation is also made from post-industrial fibres sourced from textile companies, and polyester sourced from recycled water bottles.
The uniform recycling program marks the first time Honda and its suppliers are using post-consumer textile waste for sustainable insulation material.
Increasing recycled materials in vehicles
The uniform recycling program builds on Honda’s longstanding commitment to reduce waste and incorporate higher recycled content in its vehicles. This includes working with suppliers to transform post-industrial textile scrap, such as fibres from denim, into vehicle insulation/absorption material.
In collaboration with its suppliers, Honda annually reuses over 2.5 million kgs of recycled post-industrial textile waste – equivalent to 5.6 million pairs of jeans – and 2.7 million kgs of post-consumer PET bottles – equivalent to 6 million water bottles – for vehicle sound-absorbing insulation.
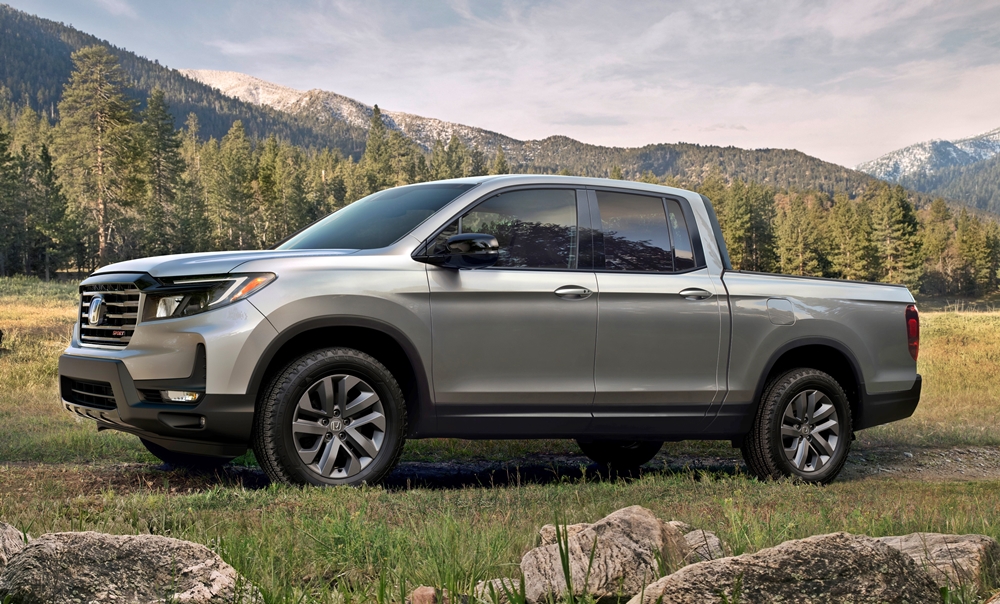
Other approaches to using sustainable materials have included soybean-based foam for vehicle headrests, recycled plastic water bottles and recycled bumpers for wheel liners, plant-based material for the seat fabric (in certain models). Even processed volcanic rocks are used for the roof liner.
Besides reducing the environmental impact of its business operations, Honda also promotes environmentally responsible business practices with its suppliers and retail dealer partners in America.