In the normal process of developing and preparing a new model, manufacturers will first complete most of the product development. Planning for the production processes – which may require new equipment or layouts – can also be done concurrently to some extent. However, unless a brand new factory is being built for the new model, it will not be possible to make the necessary changes or install equipment in preparation for producing the model.
With the current model or other models still being produced, it will be disruptive to have all the retooling work going on. This has been the case for decades and a constraint on the process of starting production of a new model.
‘Digital First’ approach
Now Mercedes-Benz has the ‘Digital First’ approach which can enhances efficiency, avoid defects and save time, marking a step-change in the flexibility, resilience and intelligence of the Mercedes-Benz MO360 production system.
MO360 is a flexible digital production ecosystem used to network around 30 Mercedes-Benz plants worldwide using real-time data. With MO360, Mercedes-Benz is able to produce electric, hybrid and combustion models on one factory line in order to scale the production of electric vehicles in accordance with market demand.
More intelligent production system
This ‘Digital First’ approach will make the production system more intelligent as well and will initially be applied at its factories in Rastatt (Germany), Kecskemet (Hungary) and Beijing (China).
“Mercedes-Benz is initiating a new era of automotive manufacturing thanks to the integration of Artificial Intelligence, MB.OS and the digital twin based on NVIDIA Omniverse into the MO360 ecosystem. With our new ‘Digital First’ approach, we unlock efficiency potential even before the launch of our MMA models in our global production network and can accelerate the ramp-up significantly.” Said Jorg Burzer, Member of the Board of the Mercedes-Benz Group AG, Production, Quality and Supply Chain Management.
Virtual ramp-up of an assembly hall
The Mercedes-Benz plant in Rastatt, Germany, showcases digital twin technology for introducing next-generation vehicles in a way which results in only minimal interruption of assembly in existing halls. With the ‘Digital First’ approach, it is possible for the new production line for new models on the MMA platform in the existing plant to be modified, configured and optimized using high-precision digital simulation techniques.
The exact position of machines, supply routes and production lines can be determined and simulated in advance without actually interrupting the production of the current models which are the A-Class, B-Class, GLA and EQA. Furthermore, production can be ramped up significantly faster when compared to a conventional planning process.
Mercedes-Benz is investing a low triple-digit million euros amount to prepare the Rastatt plant for the new models of the next-generation. The virtual ramp up in Rastatt will serve as a blueprint for the global production network which includes the cooperation plant in Beijing.
Digital twin in production
The company is harnessing its competence in the fields of software platforms, data and artificial intelligence (AI). For the plant expansion at the Hungarian site in Kecskemet, a completely digital depiction of the entire hall has been created for the first time. For this, the company relies on NVIDIA Omniverse, a platform for developing Universal Scene Description (OpenUSD) applications for industrial digitalization, such as digital twins.
The digital twin includes the entire building and the infrastructure in it, including even break areas and changing rooms for the employees. With the digital twin for production, assembly areas can be planned, retooled and inspected virtually while taking into account the need for short distances, sufficiently wide aisles, and even fire protection.
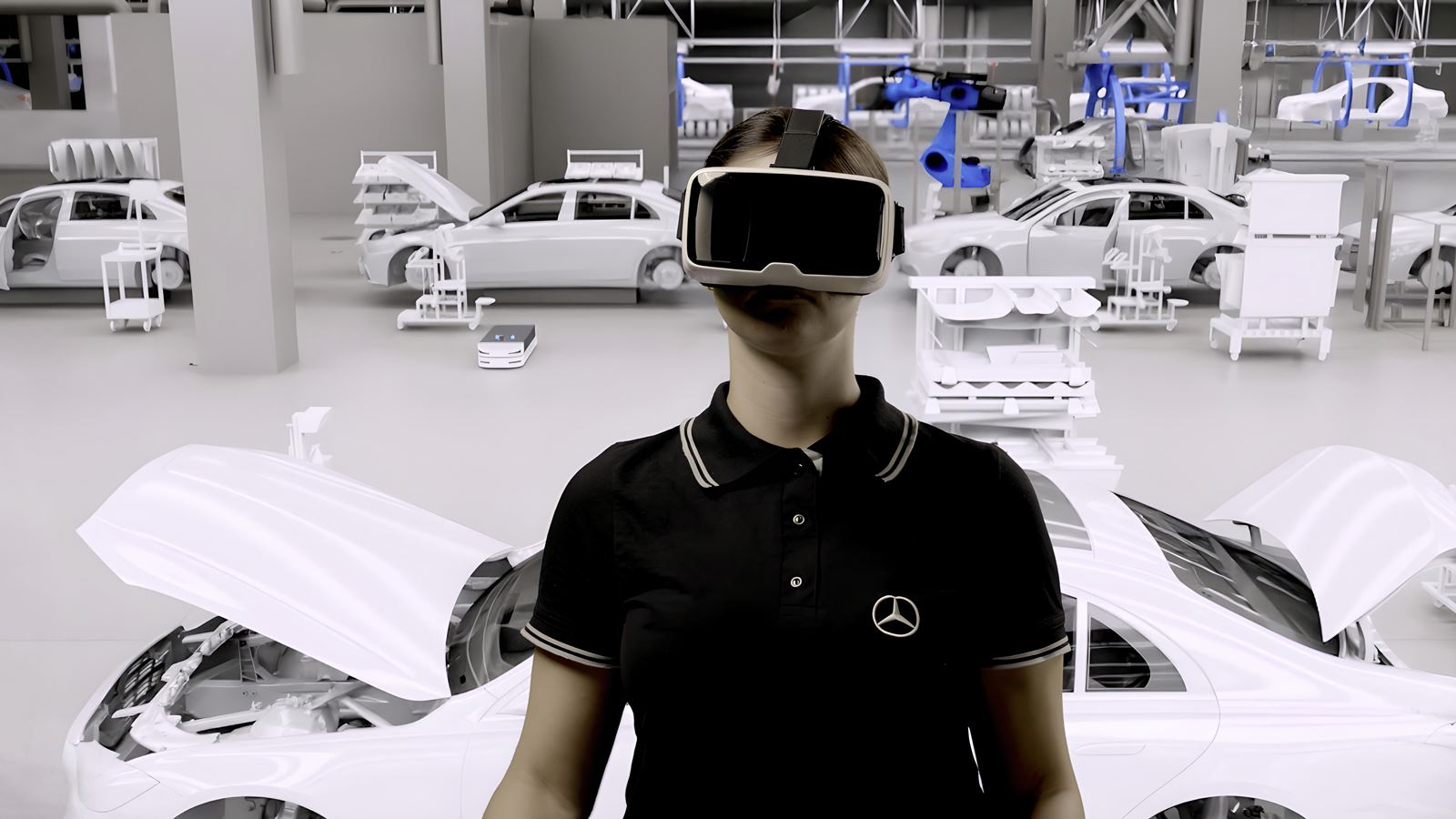
The virtual ramp-up guarantees the increased speed, transparency and flexibility of production processes without the obligation to use cost-intensive hardware. In simulation runs, savings can be conducted. By leveraging Omniverse, Mercedes-Benz can interact directly with its suppliers, reduce coordination processes by 50%.
Using a digital twin doubles the speed for converting or constructing an assembly hall – while improving the quality of the processes. With the data collected in the virtual world, assembly processes can be optimized even faster and potential errors can be detected at an early stage – without ‘real world’ interference.
Use of MB.OS
The Mercedes-Benz Operating System (MB.OS) – developed on a chip-to-cloud architecture – will be used in volume production for the first time. Necessary software will no longer be controlled by individual measures, but will be used in software packages in production that will be cyclically timed.
MB.OS in the vehicle and the technologies in production derived from it enable 10 times faster software updates than before, while simultaneously increasing the amount of data. Due to the direct link of production to the Mercedes Intelligent Cloud, all vehicles leave the production ‘always up-to-date’. In doing so, Mercedes-Benz complements its over-the-air software strategy for vehicles that have already been delivered.
Software optimizations can be rolled out globally within just a few hours, which significantly increases the safety and quality of the vehicles and ensures compliance with increased certification requirements.